A QR code for manufacturing is useful for identifying and tracking products and deliveries. It’s quite helpful in the industry as they are more customizable and hold more data than barcodes.
In fact, the QR code was originally made by its inventor Denso Wave, due to the huge demand for an upgraded barcode that could hold more data and scan better.
With QR codes, you can track the movement of goods through the supply chain—from raw materials to finished products—as well as the production processes to monitor and optimize your operations.
This makes them an efficient and convenient way to track and identify products and materials across the manufacturing, production, and delivery process—that’s why manufacturing companies should use a free QR code generator.
Table of Contents
How to use QR codes in manufacturing?
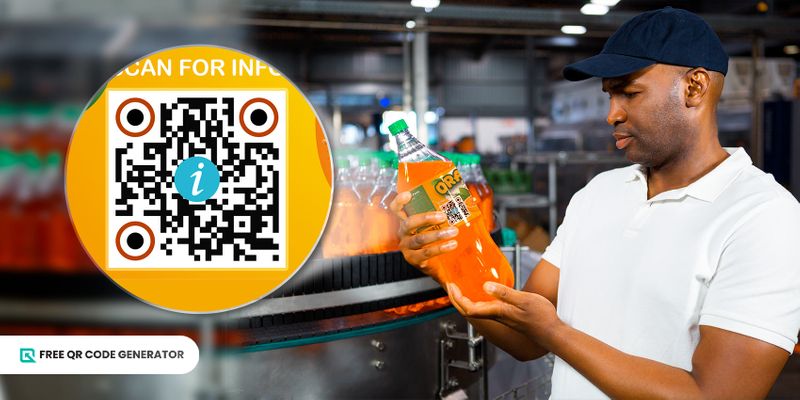
If you’re planning to incorporate QR codes in your manufacturing processes, here are some QR code ideas for businesses and manufacturing that you should note:
1. Inventory management
QR codes are great for inventory monitoring. By using a product packaging QR code on machineries, or finished goods, you can track the availability of your raw materials and refill just in time.
Since you have the option to decide on what data to keep in your code, stock levels, location, and reorder requirements would be ideal.
2. Machine maintenance and monitoring
Machines are most important in manufacturing processes, they make everything faster and convenient. If not well taken care of, it can disrupt production and cause bigger problems.
To avoid this, add a personalized QR code on your machines containing maintenance logs, user manuals, troubleshooting guides, and repair history. This way, it will be easier to track performance and effectivity of your machines.
3. Quality control
QR codes will make a difference in quality control as well. It will help provide easy-to-access information for scanners, especially those that will be sent for shipment.
For instance, whenever your code is scanned, it could lead to verify test results, production batch details, and expiry if there’s any, to ensure maximum customer satisfaction upon competition.
4. Work instructions and training
Training new workers is one of the most tasking and time-consuming part in running a manufacturing site.
You will have to go back to square one teaching and training new employees, but with a QR code, they can learn everything in just a scan. You can use a video QR code for video guides on how everything should be done.
That way, you no longer have to personally assist and train every new employees—saving your time and giving you more time to be productive on other matters.
5. Supply chain traceability
Supply chain tracking is necessary in ensuring that all parts of the product are complete from one point to another during the production process.
Through dynamic QR codes, you can ensure compliance on the operation process or keep standard requirements or documents for officer monitorings.
Different types of product identification codes
There are different ways to identify and track your products and labels. See which one has the most practical use for your company.
Barcode scanning
This is the most common type of QR code for manufacturing and production. It involves using a barcode scanner to read the QR code and retrieve its information.
Barcode scanners can be handheld devices or stationary on a fixed surface.
RFID tracking
Radio-frequency identification (RFID) technology uses radio waves to communicate with a tag or chip attached to an item.
RFID tags can be read from a distance, making them helpful in tracking items without requiring direct scanning.
Mobile QR code scanning
Arguably the most practical method of identifying your package and labels are QR codes in production. This system involves using a smartphone or mobile device to read the code and retrieve the information.
Mobile QR code scanning can be done using a dedicated QR code scanning app or the camera on the device to scan the code. It’s fast and secure, making it a low-cost but helpful part of your manufacturing process.
Barcode scanners are reliable and widely available, but they require the code to be just in the right position for the scanner to read. This can be a hassle, especially in busy, day-to-day packing and delivery schedules.
RFID tracking, on the other hand, allows for longer-range monitoring and can be more expensive to implement.
Mobile QR code scanning has to be the most convenient, as it allows quick scanning from any location. From there, delivery and production teams can easily communicate with each other.
One downside may be that it constantly requires the availability of a good internet connection to access the scanned data.
Real-life companies using QR code for manufacturing
These are some of the biggest companies that use QR code systems for manufacturers’ everyday production processes:
Nestle
QR codes have long been implemented on Nestle’s product packaging to provide customers with additional information about the product.
By scanning this retail QR code, customers can access information about the product’s ingredients, nutritional value, and environmental impact.
Toyota
Toyota has seen the importance of using QR codes in its manufacturing plants. They use QR codes for car parts to improve their tracking and identification.
QR code tracking helped Toyota monitor the movement of goods through the supply chain and improve the efficiency of its operations.
Caterpillar
Known for its fleet of construction equipment, Caterpillar, better known as CAT, has implemented QR codes on its heavy machinery to improve maintenance and repair processes.
Technicians can access detailed information about the equipment, including repair manuals and parts lists, by scanning QR codes on the machinery.
Key considerations for implementing QR code
Here’s what you should be mindful of when using QR codes in your labels—to ensure effectiveness:
Training employees
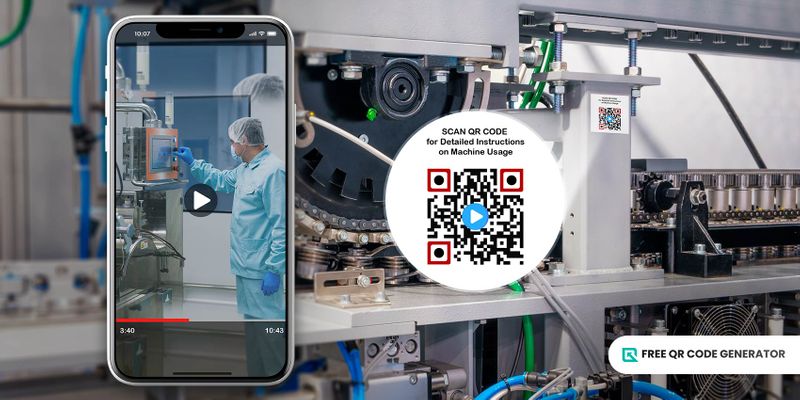
Proper training is essential to implement any new system successfully.
It is important to ensure that employees understand how to use your QR code for manufacturing plants on their work phones and are familiar with the procedures for scanning and handling customized QR codes.
This includes following data security protocols to eliminate threats to your company’s intellectual property rights and other sensitive information.
Integrating the system into existing processes
When your employees fully understand the importance, how to make these codes and the correct use of free QR codes in your regular operations, you can seamlessly integrate QR code systems.
This is one big way of minimizing errors and disruption to ensure a smooth adoption.
For instance, you can create a roadmap on how the QR code for car parts system will fit into the company’s current workflow and make any necessary adjustments as you go along.
Ensuring data security
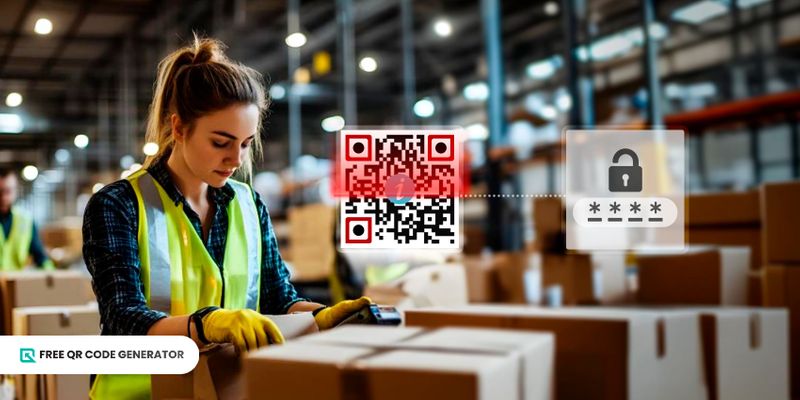
Choose a QR code maker platform that prioritizes sensitive data protection above everything else.
With free dynamic QR codes’ capacity for tracking, you can use this QR code production tracking tool and add a password for better security.
Use secure, state-of-the-art QR code software and constantly monitor the work devices used to scan them.
This may involve implementing more security features such as encryption or secure login protocols.
Choosing the right QR code provider
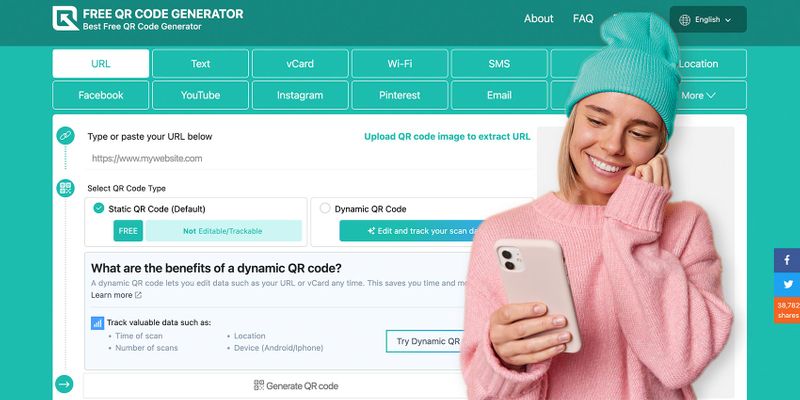
Of course, it is essential to choose a reputable and reliable free QR code generator to ensure that the system is reliable and easy to use.
It is also important to consider the provider’s customer support and the level of assistance they can offer in case of any issues or questions.
Our QR code software surely checks all these boxes, as every business’ shared information is critical. One faulty QR code can easily cause huge setbacks in the production and delivery process.
Choose the correct type of QR code system for manufacturers
Make a list of the things you need to be properly labeled and organized.
As you now know, several QR code systems are readily available, each with its benefits and drawbacks.
It is essential to choose the method that best fits the company's needs and budget.
Streamline your production process using QR codes
Setting up a proper QR code for manufacturing can greatly change the game for your manufacturing and production process.
From tracking the movement of goods in your supply chain to providing detailed information about products and materials, QR codes are free and low-cost but valuable tools for improving efficiency and streamlining your operations.
Several QR code systems are readily available, including barcode scanning, RFID tracking, and mobile QR code scanning, so choose the method that best fits your company’s needs.
If you’re still in doubt, you can just check your grocery aisle and see all the great case studies of brands that have effectively implemented a QR code system for manufacturers.
You only need to consider these important details:
- Choosing the correct type of QR code system
- Integrating the QR code system into existing processes
- Training employees to adapt to the QR code integration
- Ensuring data security across the manufacturing process
By following best practices and working with a reputable free QR code provider, companies can successfully implement QR code systems and reap its practical benefits.
Use Free QR Code Generator today and make full use of its features to improve your processes in manufacturing.